Podcast: Play in new window | Download
Note: Scroll down to see who I unexpectedly met in Florida this past week!
Now for the Prebuy… it was some months ago, and I did a prebuy inspection on a nice airplane on behalf of the buyer.
I also became good friends with the owner / seller, for which I was grateful, because sometimes these can end up being sticky situations.
The owner / seller (who is a really great gentleman) seemed to think his airplane was nearly perfect, and there should be very little wrong with it.
And by all means, it was a very nice airplane indeed. So much so, that if I was buying it, I’d be thrilled!
Nevertheless, I found some things that needed attention.
Listen to the episode to hear about the things I noted, which I categorized into three parts:
- Significant Items
- Miscellaneous Observations
- Items to consider during next annual inspection
I’m not going to list them all here, but I talked about them in the audio for this episode.
Here’s a photo of one item I found… the right flap forward rib had a large crack in the leading edge – a very common problem on Bonanzas. (The flap was sent out for repair, and reinstalled, as part of the selling process.)
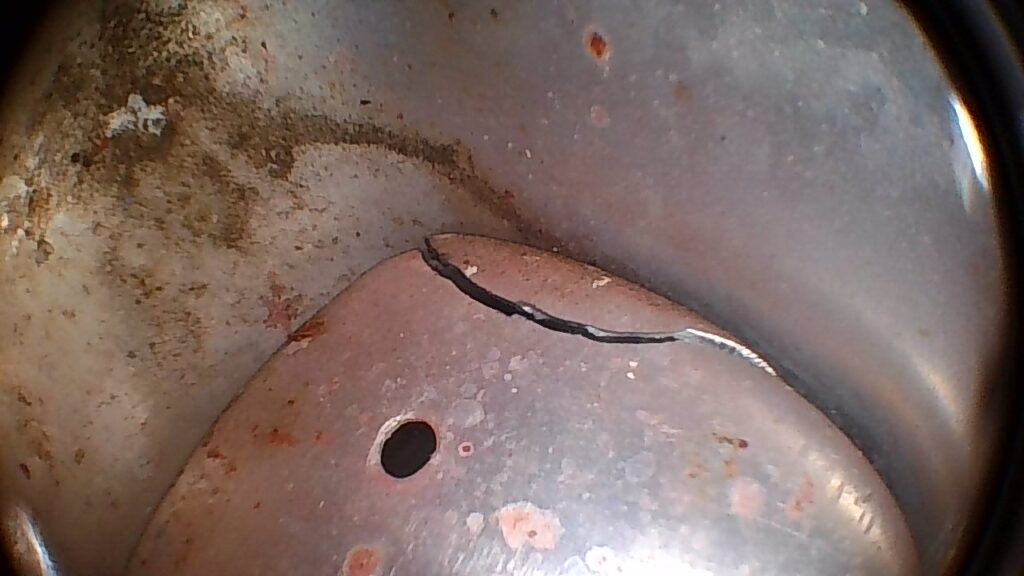
This crack can be seen by looking outboard and forward inside the open inspection hole in the flap in the following photo:
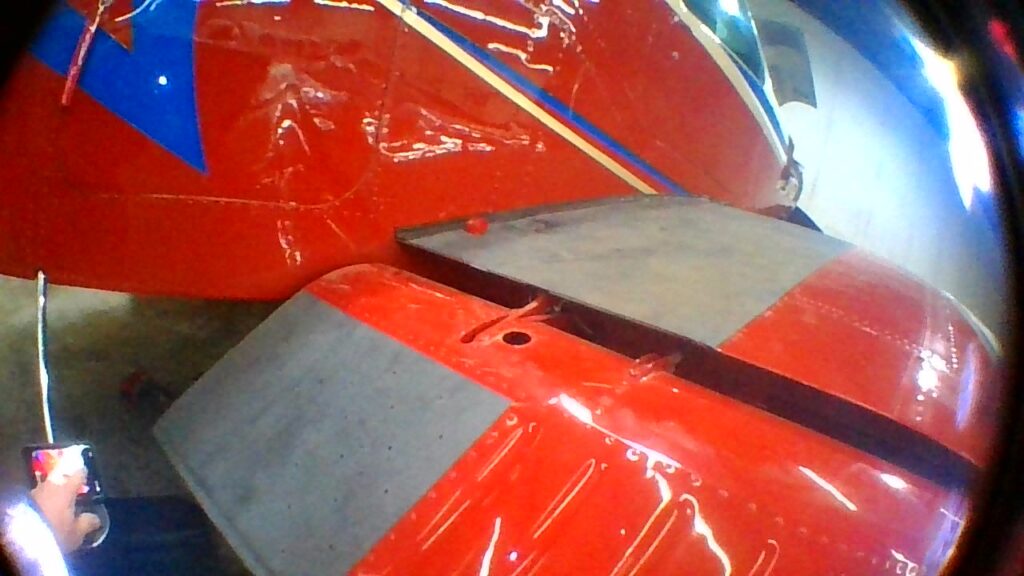
The following photo shows the forward nose gear rod end that was replaced, along with the nose gear down spring and some other hardware (note the small grease zerk in the side of the rod end… rod ends that are drilled for a grease zerk have been known to fail, and it’s wise to replace them with the solid type.)
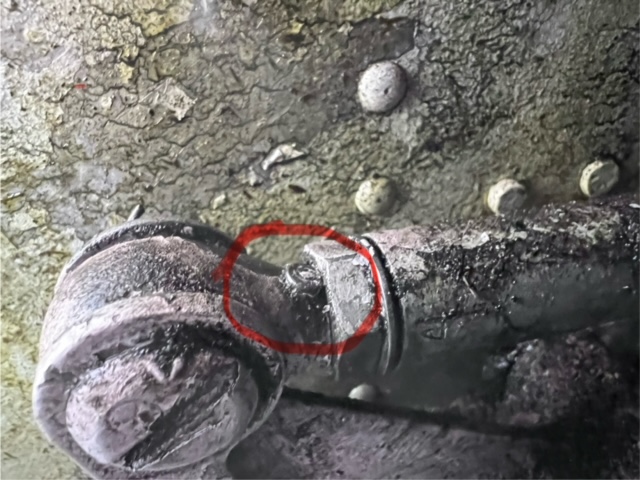
Note: American Bonanza Society (ABS) recommends replacing all three rod ends for the Bonanza nose gear system every 2000 hours.
For me, the prebuy was a great experience, and I’m hopeful both the seller and the buyer feel the same way.
In my estimation, we took a really nice airplane, and made if even better… and that makes me happy!
How about you? Is your airplane perfect?
One way to see how perfect it is would be to get some other eyes on it from time to time… take it somewhere different every few years for the annual inspection.
Then, when it comes time to sell it, perhaps it will be just a little closer to perfect!
Now for my huge surprise in Florida this past week… I met a very fine gentleman at the Orlando Executive Airport, and even got a photo with him:
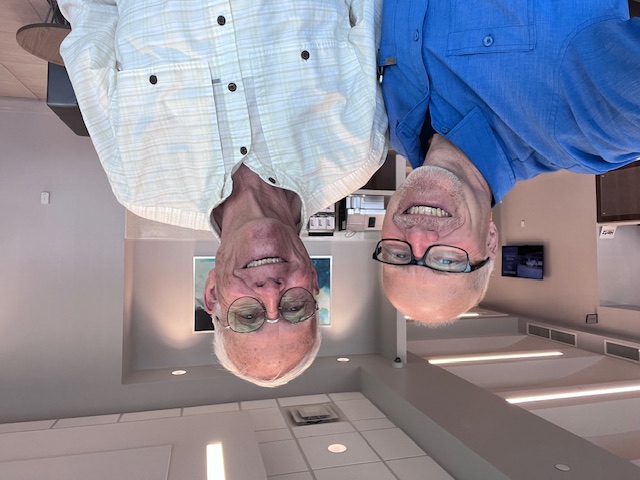
This is Mr. Bob Showalter, of the Showalter Flying Service in Orlando, which the family sold back in 2015.
I was grateful to meet such a fine gentleman that day, and to learn more about him and his family, and how they have contributed in such a huge and impacting way to the world of aviation.
So many people have asked me over the years if I was related to the Showalters who have the FBO in Orlando, and my answer will now be, “Not that I’m aware of, but if I was related to them, I’d be proud!”
If you’re interested in some fascinating history of Bob’s family and Showalter Flying Service, here’s a link with all kinds of interesting information, as well as a large assortment of really fun photos from years ago.
And here’s another one:
Enjoy!
And Mr. Bob, it was a real pleasure to meet you sir! I was very inspired to hear you are still going strong and still flying a jet with your son!
The post “239 – When Your “Perfect” Airplane Gets a Prebuy” appeared first at AirplaneOwnerMaintenance.com
Recent Comments