Podcast: Play in new window | Download
AD 2017-14-04 affects a huge list of Piper models, including Cherokees, Arrows, and Saratogas.
But before we get into that, I wanted to give an update on the alternator brushes mentioned in episode 069. Here are some pictures of the new brushes I installed in that alternator:
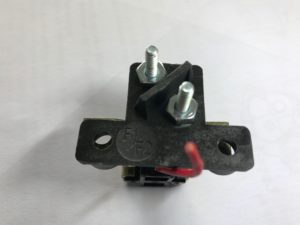
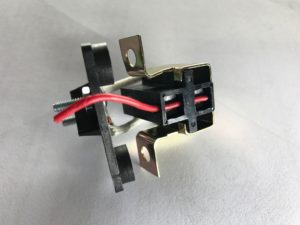
That little red wire holds the brushes out of the way while the brush holder is installed in the alternator. Then, after it’s in place and the screws are tight, the red wire is pulled out gently, and the brushes snap down against the slip rings in the alternator.
After installing this new brush assembly in the left engine of that twin Cessna I was working on, the charging system was back to normal!
Now for the new AD on Piper oil cooler hoses. AD 2017-14-04 supercedes AD 95-26-13.
I discovered this new AD recently while performing an annual inspection on a Piper Archer. The oil cooler hoses were still in relatively good condition, although they had over 1200 hours on them. (This airplane gets flown a lot.)
These were not TSO-C53a, Type D hoses, so they had to be changed. The good thing is, we ordered and installed new, Type D hoses, so that terminates the AD for this airplane.
This AD has a lot of information in it, and it can be a little confusing to figure out, but the bottom line is, if you have TSO-C53a, Type D hoses, they are not affected by this AD. However, if you have Type C hoses, or any other hoses, they need to be inspected at certain intervals, and then replaced when they have either 8 years, or 1000 hours, on them.
How can you tell if you have Type D hoses? Just look at the metal tag on the hose assembly. If it says Type D on that tag, your hoses are not affected by this AD. Generally, Type D hoses will be either the teflon hoses, with smooth, brown, exterior and a tag that says “Type D,” or, hoses with orange firesleeve, that also have a tag that says, “Type D.”
Back in 1996, another document that was issued by the FAA, was SAIB ACE 96-01, which offered some AMOC’s (Alternative Method Of Compliance.) AMOC #1 gave the option to terminate the AD with Type C AND Type D hoses, as long as the oil cooler was mounted at the rear of the engine, and there were no defects noted on the hoses.
But with the new AD, that AMOC is no longer approved as a method to comply with the new AD.
So I had to change those hoses in that Archer… oh well, they should last a very long time! And since we installed Type D hoses, the AD is now terminated in that airplane.
If you want to dig deep and learn some detail about hoses, how they are made, and the differences between type C and type D hoses, here is an AOPA article that is quite educational:
https://www.aopa.org/news-and-media/all-news/2006/january/01/airframe-and-powerplant
Here are a few recommendations to consider when it comes to engine hoses, regardless of what type of airplane you have:
- Although not required for part 91 operators, good idea to change them every 8 or 10 years. Many airplane engine hoses are 20 or 30 or more years old… you’re taking chances to let them go that long.
- Make sure there is clearance between hoses and any exhaust component.
- Verify hoses are not bent too tightly.
- Always be looking for any leakage… esp. at hose ends.
- Verify all hose B-nuts are tight, with torque putty applied.
- If you move a hose to the side, and you hear it creaking, it’s probably old and needs to be changed.
- Even though the brown, teflon hoses are sometimes described as having no life limit, it’s still a good idea to change them at a reasonable frequency.
Now for one final thing that surprised me the other day. I was inspecting another Piper Archer, and part of the inspection is draining the fuel tanks. After collecting some liquid from the left fuel tank, I noticed it did not look like Av Gas… and it did not smell like Av Gas. So I continued draining until I got fuel… I had drained almost 1/2 cup of water out of that tank!
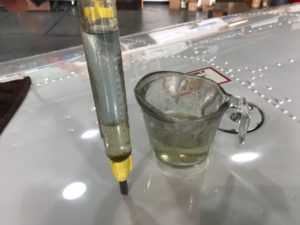
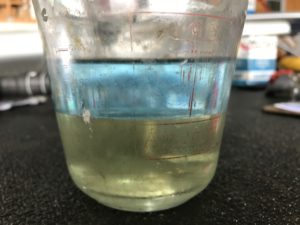
It was one more reminder for me to avoid complacency, and keep doing the routine, but important items.
Here’s another interesting thing about that left fuel tank. The cap was broken… perhaps this was the reason it did not seal well, and let water in! (A new cap will be installed.)
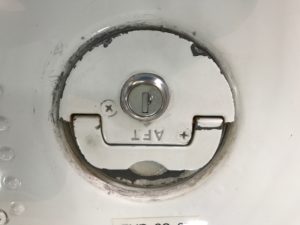
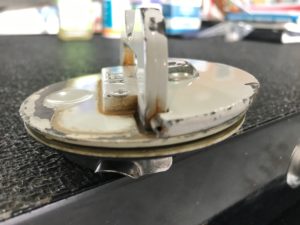
Thanks everyone! See you next time!
Recent Comments