Podcast: Play in new window | Download
(If you’re in a hurry, scroll down to see the tiny little chafed wire that caused this whole conundrum.)
Now here’s the story…
This landing gear relay breaker had been popping intermittently:

It came time for annual inspection and we decided to replace the breaker with a new one, in order to rule out a faulty breaker, and attempting to minimize long and frustrating labor for troubleshooting.
Good thing, because as it turns out, there was a loose screw in the landing gear motor breaker next to this one, which would not have been discovered if we had not replaced the relay breaker… check out the loose screw:

It was obvious some arcing had occurred due to the poor connection:
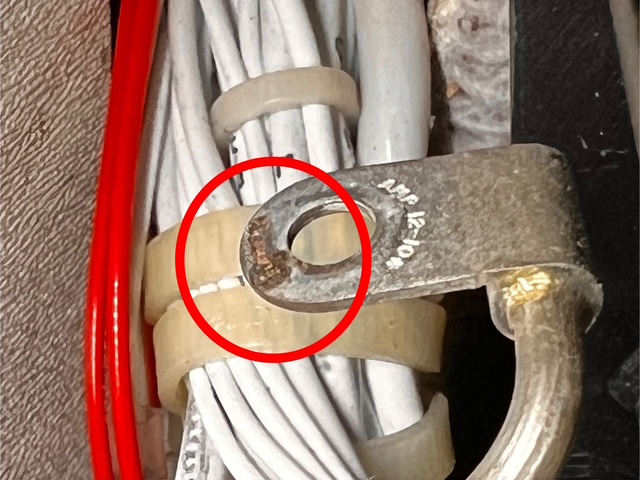
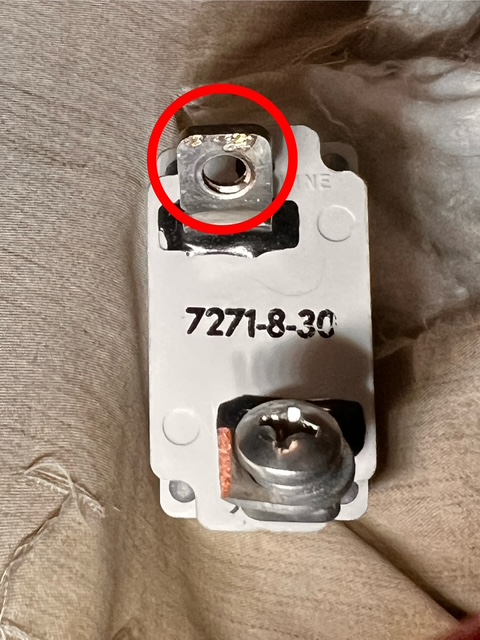
Unfortunately, tightening the screw in the 30 amp motor breaker, and installing a new 5 amp relay breaker, did not fix the problem.
Back up on jacks for more troubleshooting:
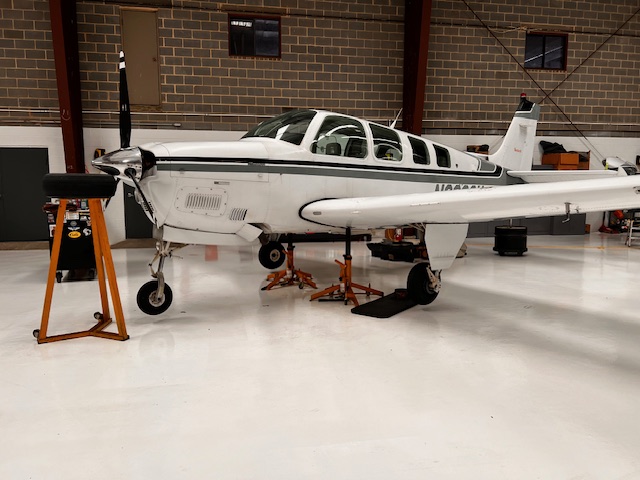
Todd, the airplane owner, posted in BeechTalk about the situation, and we got some good feedback.
Meanwhile, I took a good look at the wiring in the main gear wells, especially the squat switch wiring… no issues found.
So I called the American Bonanza Society (I love their tech support, and it always reminds me of the exceptional value of being an ABS member, even as an A&P/IA.)
Curtis Boulware discussed the wiring diagram with me and pointed me to some things to check:
- Disconnect the C1 terminal from the gear relay and test… nope, it’s not that:
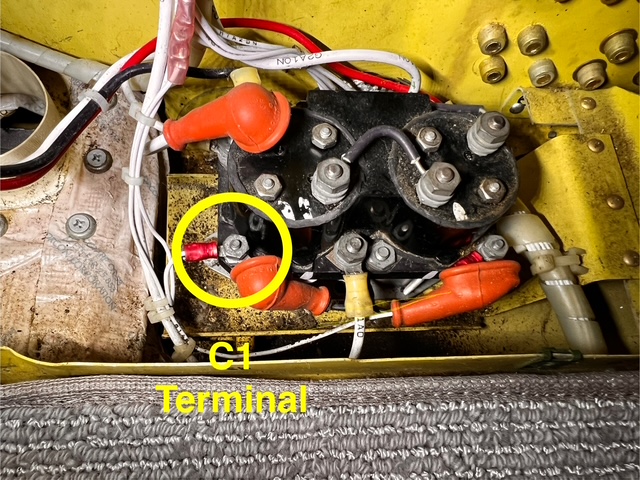
- Disconnect plugs in gear wells and test… nope, it’s not that:
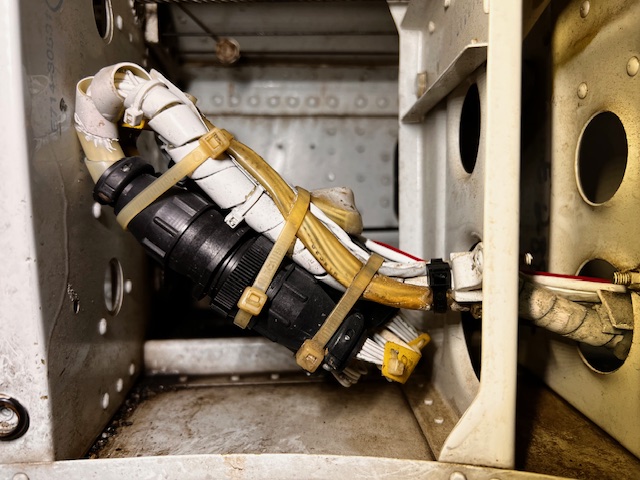
- There’s a circuit board located under the copilot panel above the right rudder pedal:
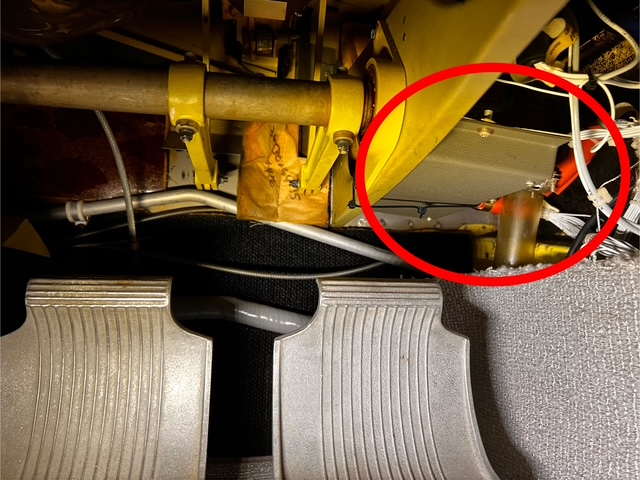
Aha! Now we were getting closer.
After removing the circuit board from its mounting position and disconnecting the P1 plug, the relay breaker no longer popped when gear was selected up.
But why?
I was beginning to wonder if we would need to have the circuit board repaired or replaced… and who knows how much one of those would cost!
And then my eyes landed on something that did not look quite right.
It was a spot on a tiny little wire.
After closer examination, sure enough, this little wire had chafed through the insulation and some of the internal strands of copper wire were visible:

But what had it been chafing on?
Finally, I saw it… a burnt spot on the sidewall of the airplane:
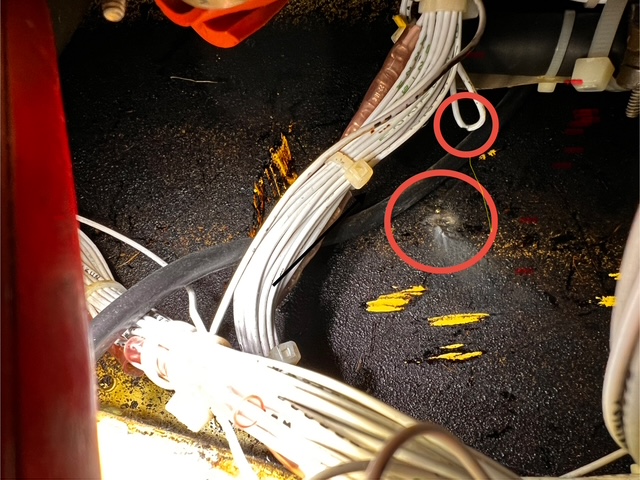
Perhaps this wire had been chafing for many years and finally wore through the insulation. (The little loop of wire had not been adequately secured into the wire bundle, which allowed it to touch against the aluminum sidewall of the fuselage.)
It was the little G43A20 jumper wire that connects 2 pins in the P1 plug.
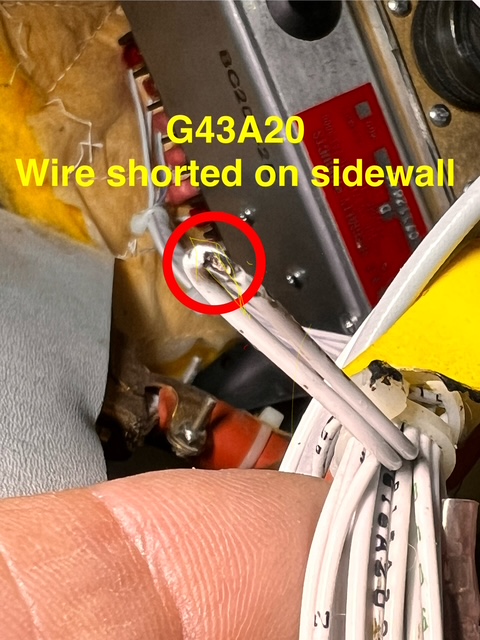
After removing the bad spot in the wire, splicing it back together, and securing the wiring, the landing gear system worked perfectly.
And if you’re curious like me, here’s a peek inside that circuit board under the copilot panel near the outboard rudder pedal:

I’m glad we didn’t have to replace that thing!
(To hear the full story on this one, be sure to listen to the audio for this podcast episode.)
The post, “252 – Why Does the Bonanza Gear Relay Breaker Pop?” appeared first at AirplaneOwnerMaintenance.com
Recent Comments