Podcast: Play in new window | Download
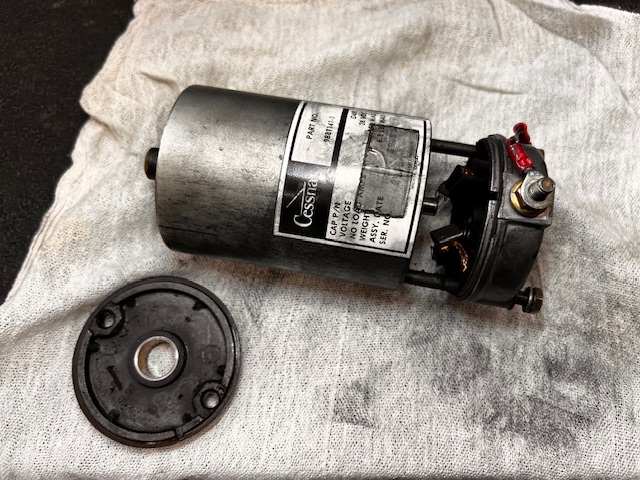
This story begins with a squawk from the owner. It went something like this:
“When I fly my airplane, on the first landing gear retraction, the gear begins to move and then the “gear pump” circuit breaker pops. After I reset the circuit breaker, the gear retracts and extends normally with no further problems the rest of the trip.”
Weird…
What could be wrong?
It was my job to figure out what was going on.
I put the airplane on jacks and selected “gear up.”
Sure enough, the gear began to move and after a short time, it stopped mid-travel and the “gear pump” circuit breaker popped.
For once, the problem happened just like the airplane owner had reported.
I checked each gear leg for any binding, and everything appeared nice and free to move.
After evaluating and thinking through the situation, I decided it was a reasonable possibility there was an internal problem in the electric motor on the landing gear power pack.
I removed the motor and quickly discovered it was full of debris. Take a look at the brush housing:
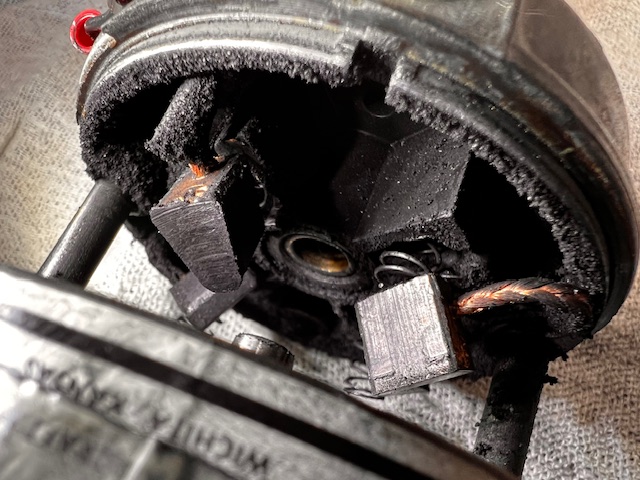
Amazingly, a can of contact cleaner and some compressed air produced a quick transformation… and the brushes actually had lots of good material remaining:
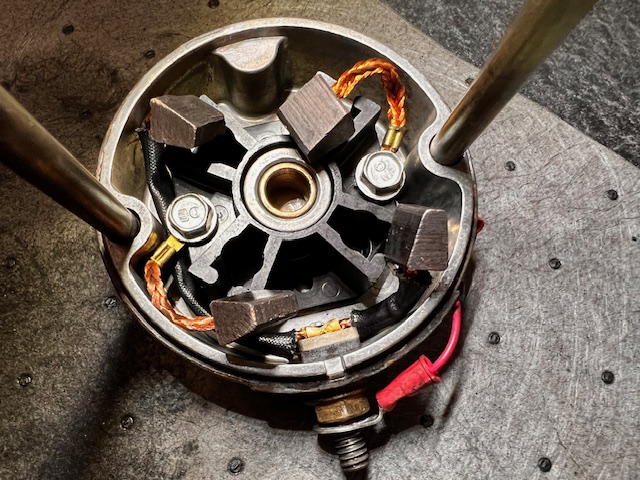
The commutator segments were in similar rough shape when I first disassembled the motor:
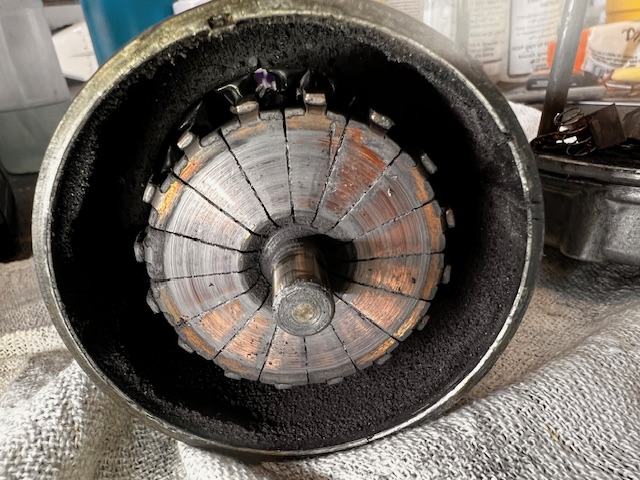
But some Scotch-Brite, contact cleaner, and compressed air freshened up this area as well:

The armature housing also had a large amount of debris to be removed:

I didn’t think to take a photo after cleaning, but it turned out very nice as well.
Before disassembling the motor, I thought we might end up replacing it with an overhauled one.
But after seeing how well the motor was made, how simple it was, what good condition the brushes and other parts were in, and how easily it cleaned up, I realized it would likely be good to go for a long time, and I decided to reinstall it.
And here’s the motor after reassembly, along with one of my grubby hands 🙂
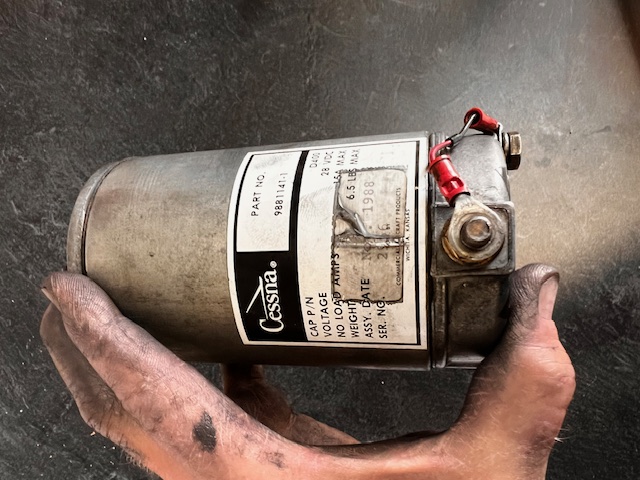
Here’s the landing gear power pack area that’s accessible near the copilot’s feet after removing the little plastic cover on the side of the console: (these photos are before I reinstalled the motor.)
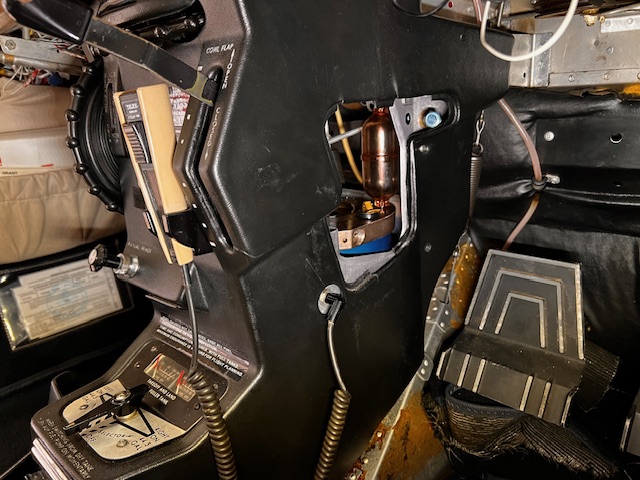
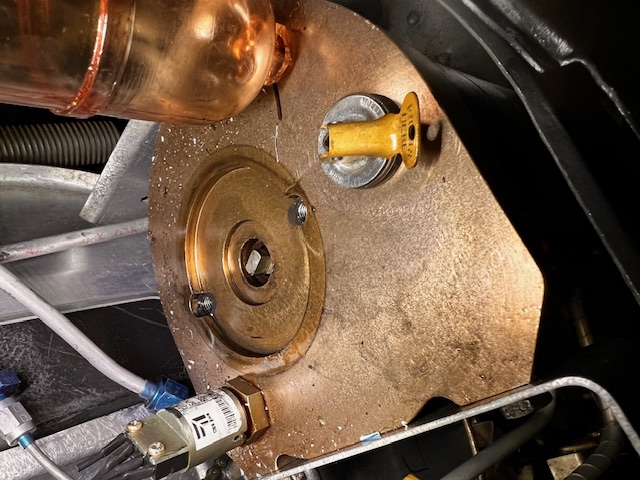
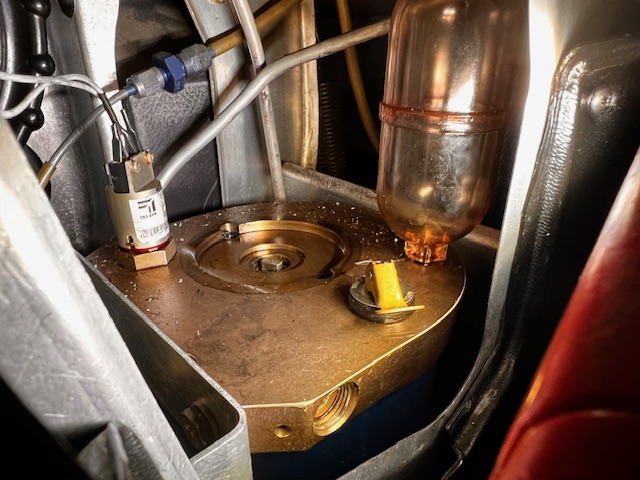
Before reinstalling the motor, I put some black electrical tape around the end seams to keep the housing from coming apart (there are 2 long 1/4 inch bolts that go through the length of the motor and attach it into the drive area on the power pack.)
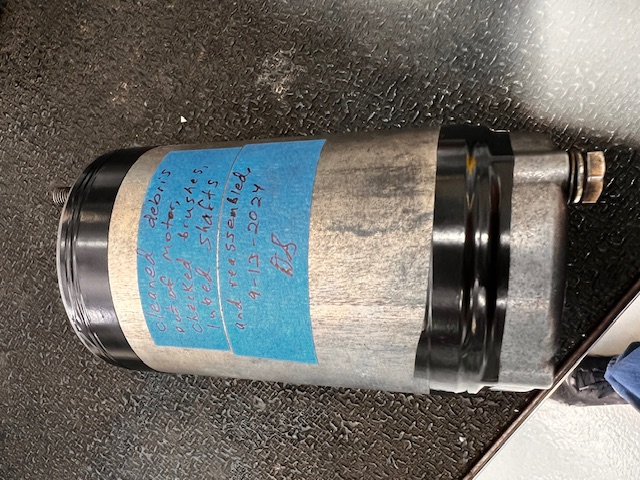
After everything was back together, I ran the landing gear, and it performed flawlessly!
Now, the real test will be to see what happens the next time the owner flies his airplane. Until then, I’m hopeful for a good report.
Sometimes, we do need to just replace parts on airplanes… but sometimes, we can be a real mechanic, and dig in and repair an existing component!
In this case, I’m figuring I saved this owner a chunk of change on this repair.
One final item: when the airplane was in the shop, it became really obvious the right brake caliper was leaking… check it out:
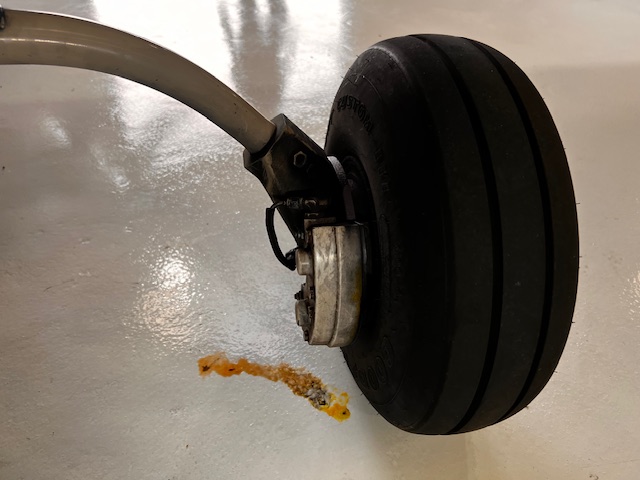
A couple new o-rings and some brake linings took care of this squawk as well.
Now it’s time to go fly!
The post, “246 – Parts Changer or Real Mechanic? Cessna-210 Landing Gear Motor Story” appeared first at AirplaneOwnerMaintenance.com
Recent Comments