Podcast: Play in new window | Download
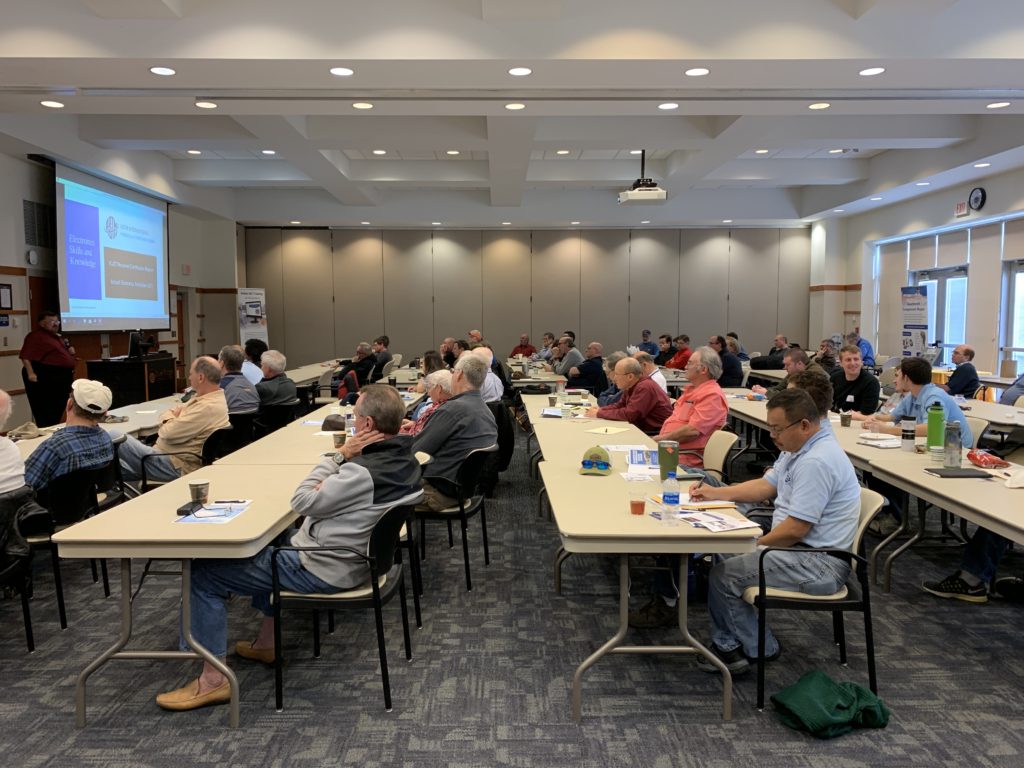
Yesterday, I had an opportunity to present a talk at our local IA renewal seminar about exhaust valve borescoping.
I shared some of my favorite pictures – the ones that demonstrate how critically important borescoping is, and that compression testing alone is not sufficient.
The following three examples are especially startling, since they showed a compression test of at least 60/80, but were in imminent danger of in-flight failure:
The FIRST ONEis from a Continental engine in an A36 Bonanza. Notice the green area at 9:00, indicating that area was in danger of a piece breaking off the edge.
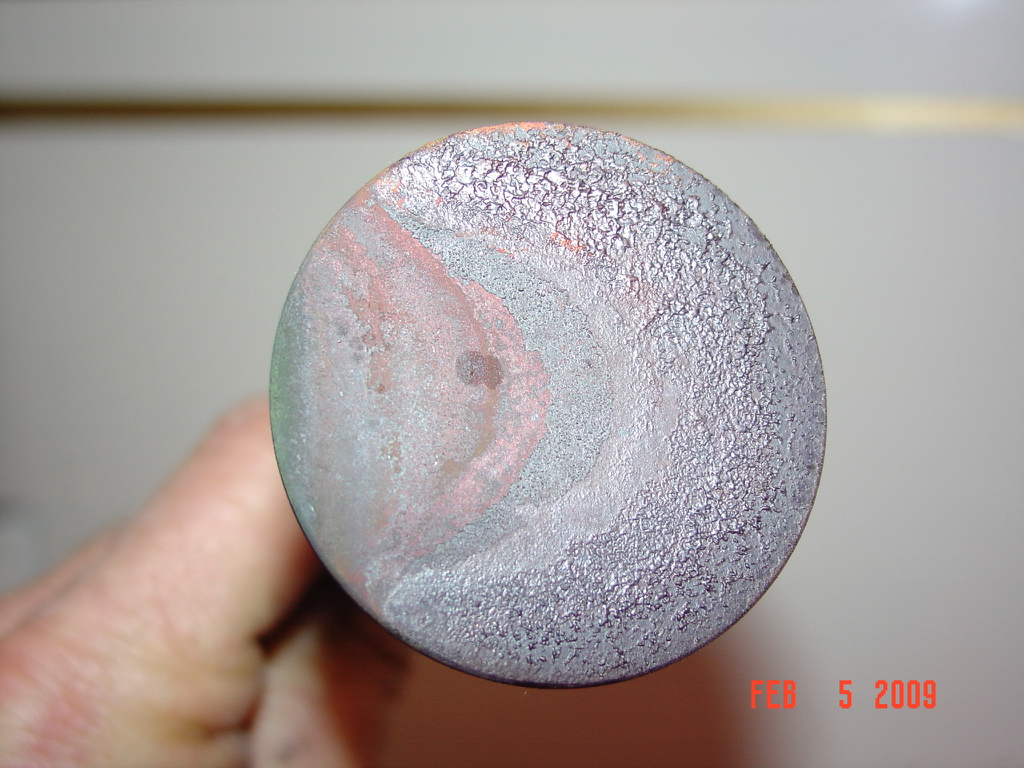
The SECOND ONEis from another Continental engine, also an A36 Bonanza. The compression of this one was 61/80, but there was a chunk missing from the edge, with a crack toward the center of the valve!
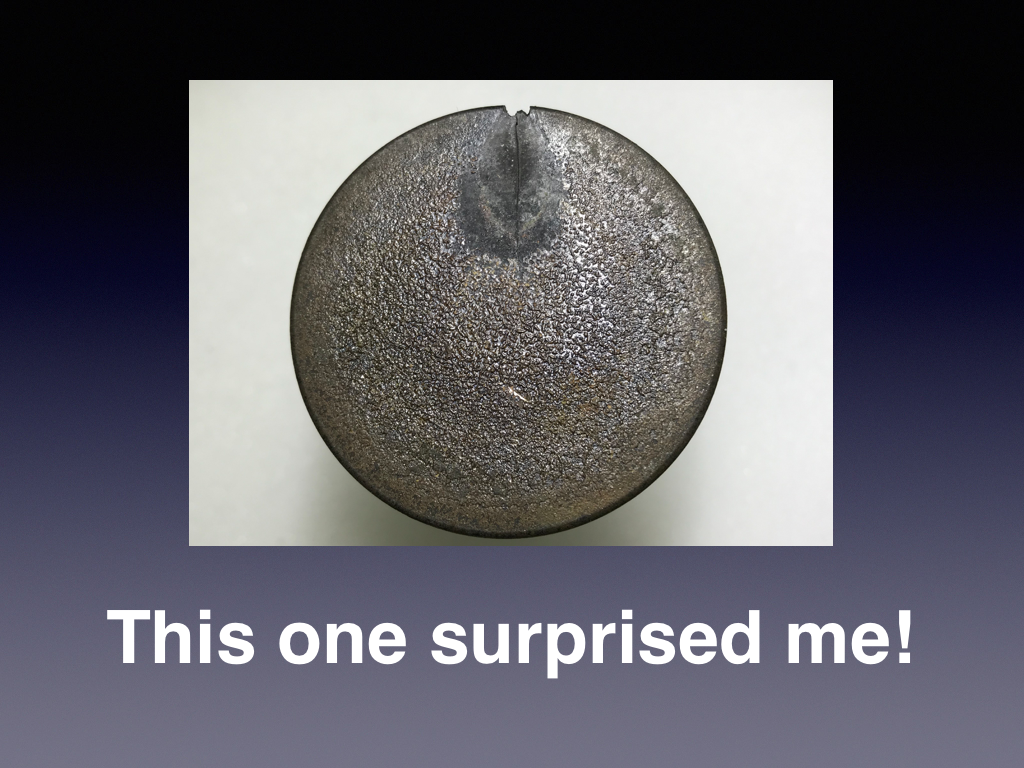
The broken edge still had enough area to seal for a compression test:
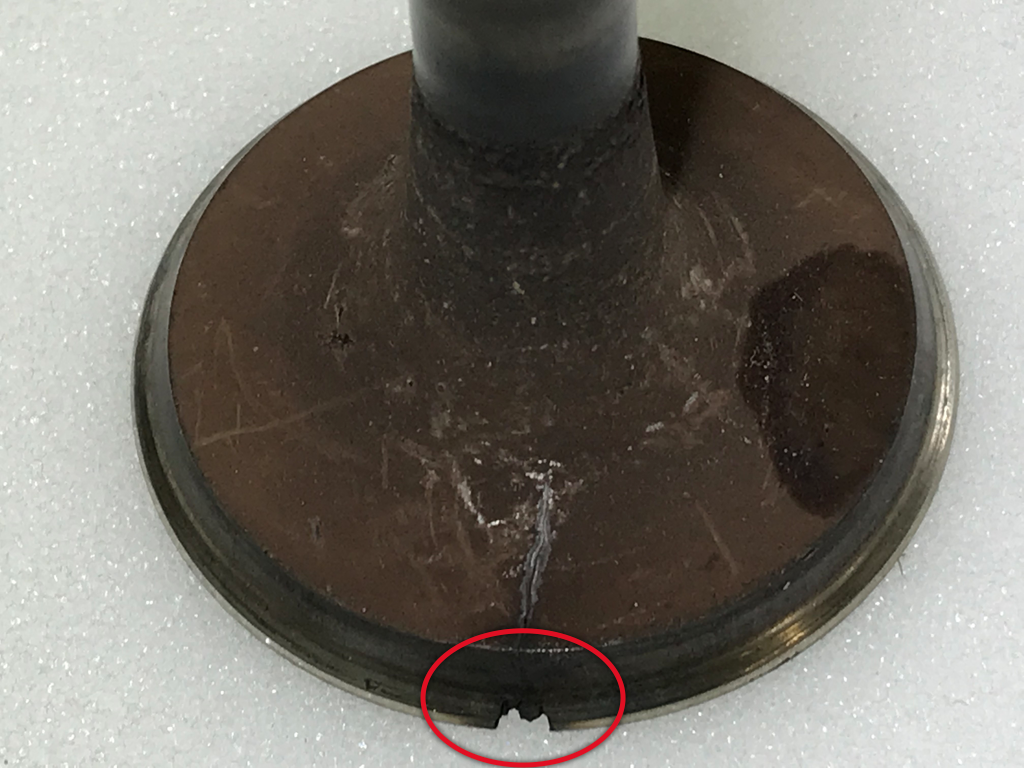
And the THIRD ONE was from a Lycoming engine in a Cessna 152. Take a look:
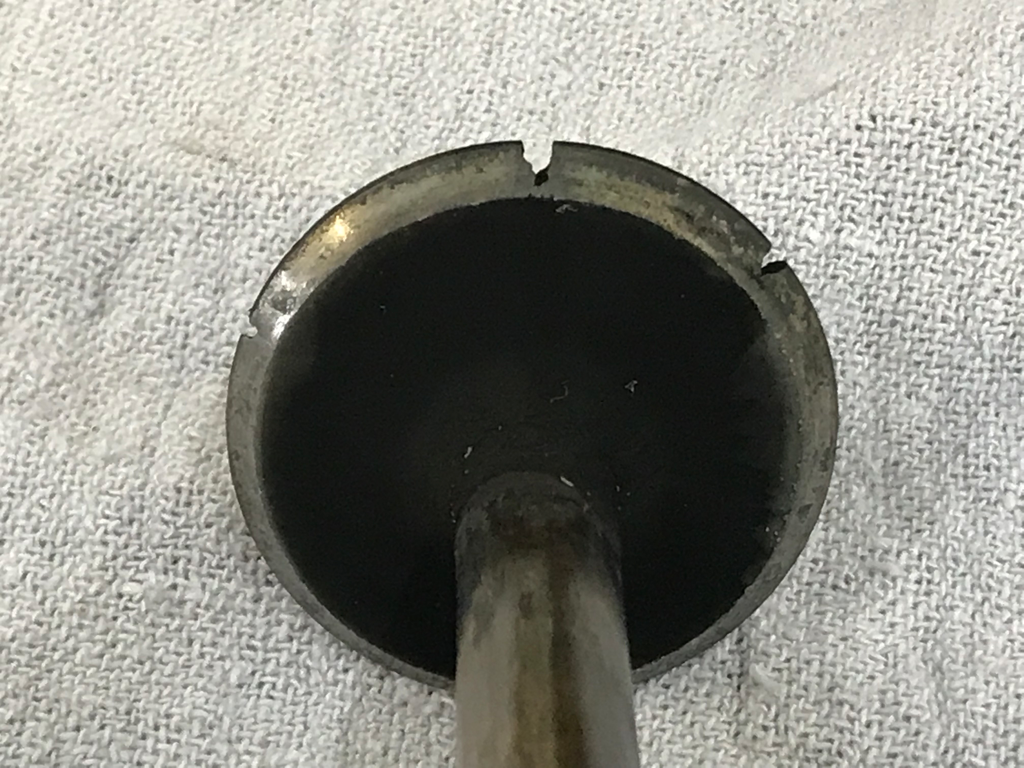
In the previous three examples, the borescope was absolutely necessary to discover these dangerous and unairworthy exhaust valves.
For comparison purposes, the following two pictures are examples of healthy exhaust valves:
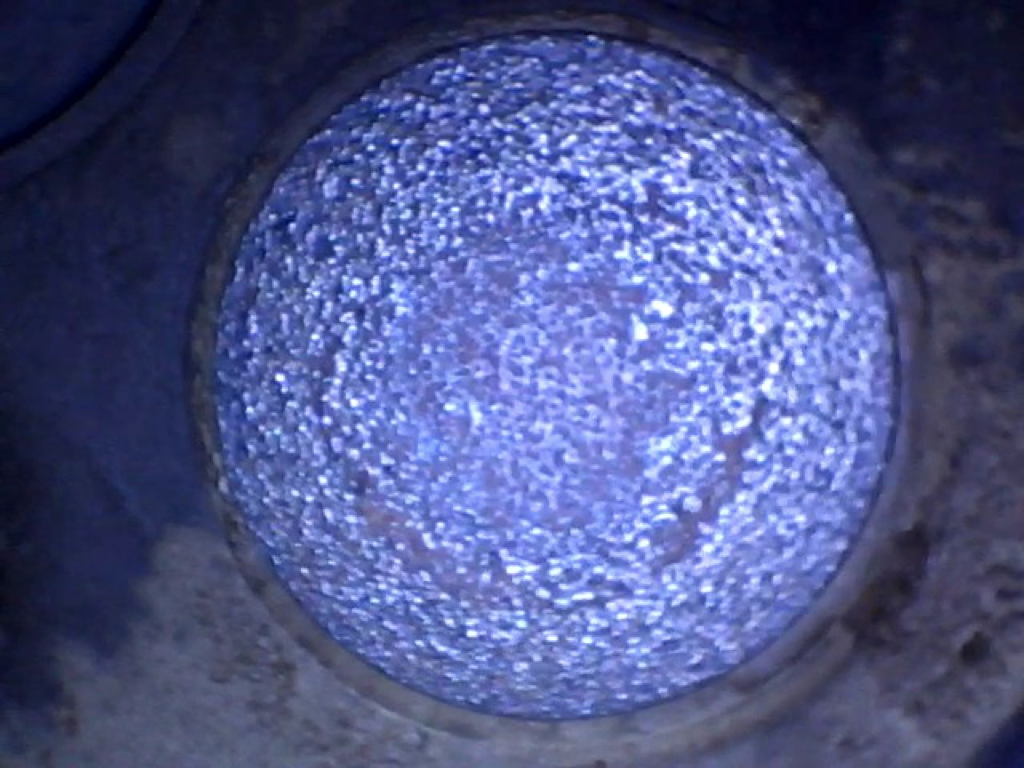
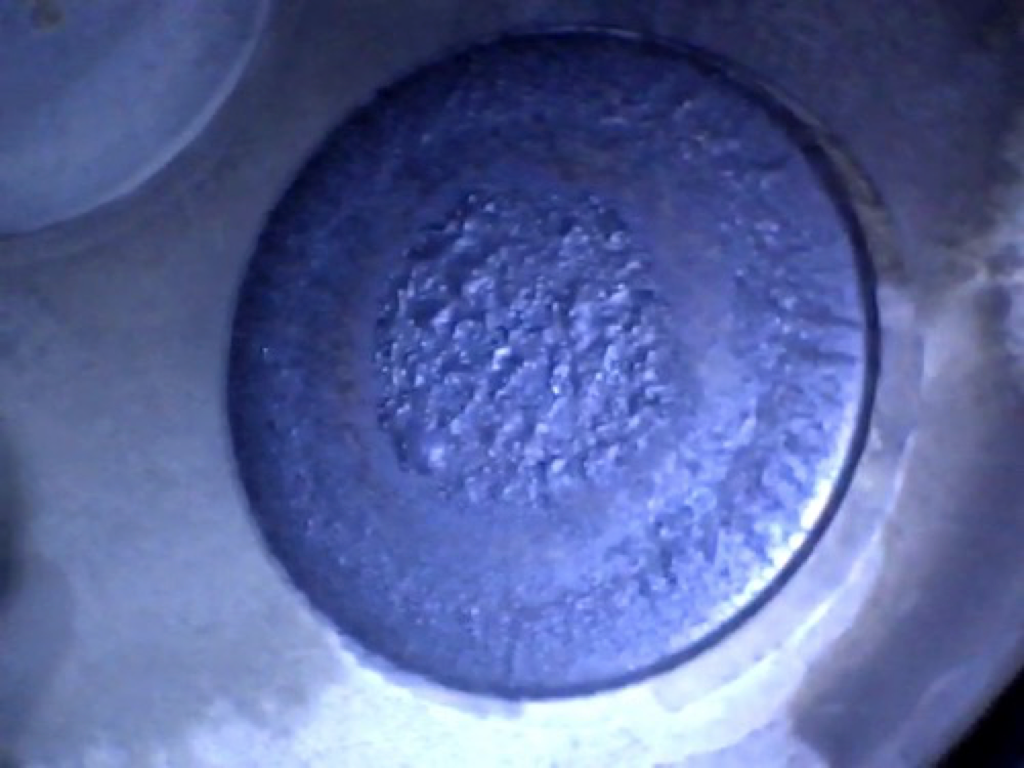
I also shared some pictures of valves that other people have removed from their engines.
The following is from Sylvan Martin’s Grumman Tiger with a Lycoming O-360 engine. Sylvan was able to land safely after his engine ran slightly rough. He said, “My opinion is that cylinder 1 would have been noticeable at a minimum of 150 hrs before it deteriorated to the point of cracking that far across the face… Compression check will help w/ ring problems, but our family’s experience in industrial diesels (power generation) is that rings fail slowly/predictably while valves fail suddenly/catastrophically…..”
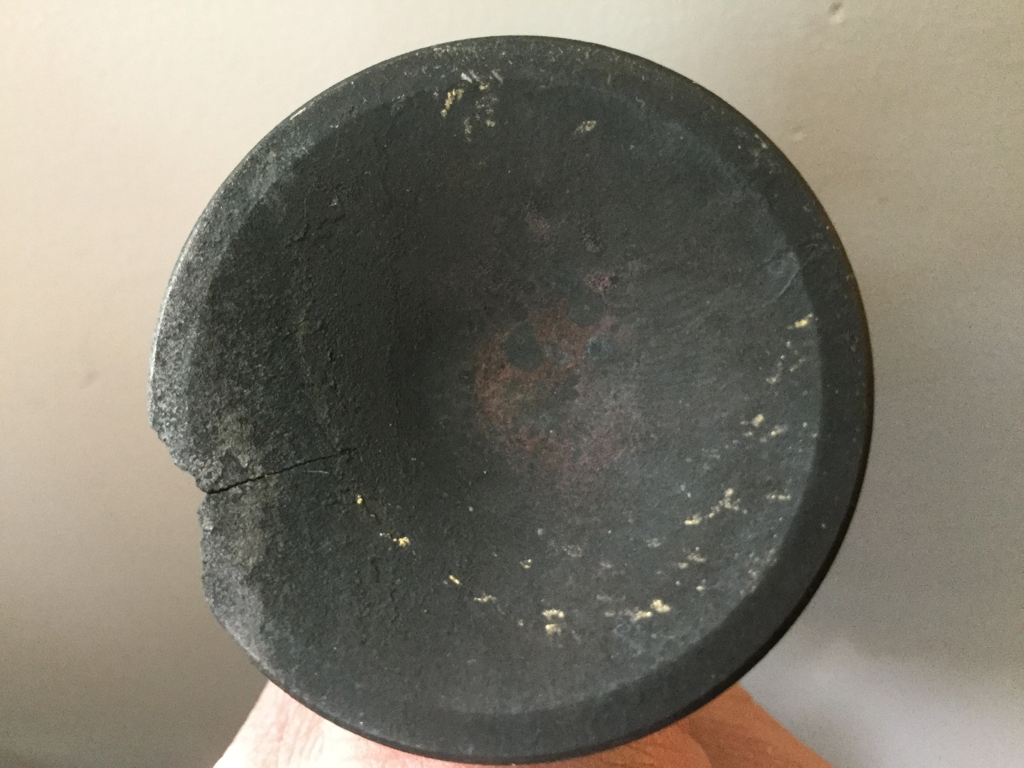
He later had to change two other cylinders, after the borescope indicated they were burning:
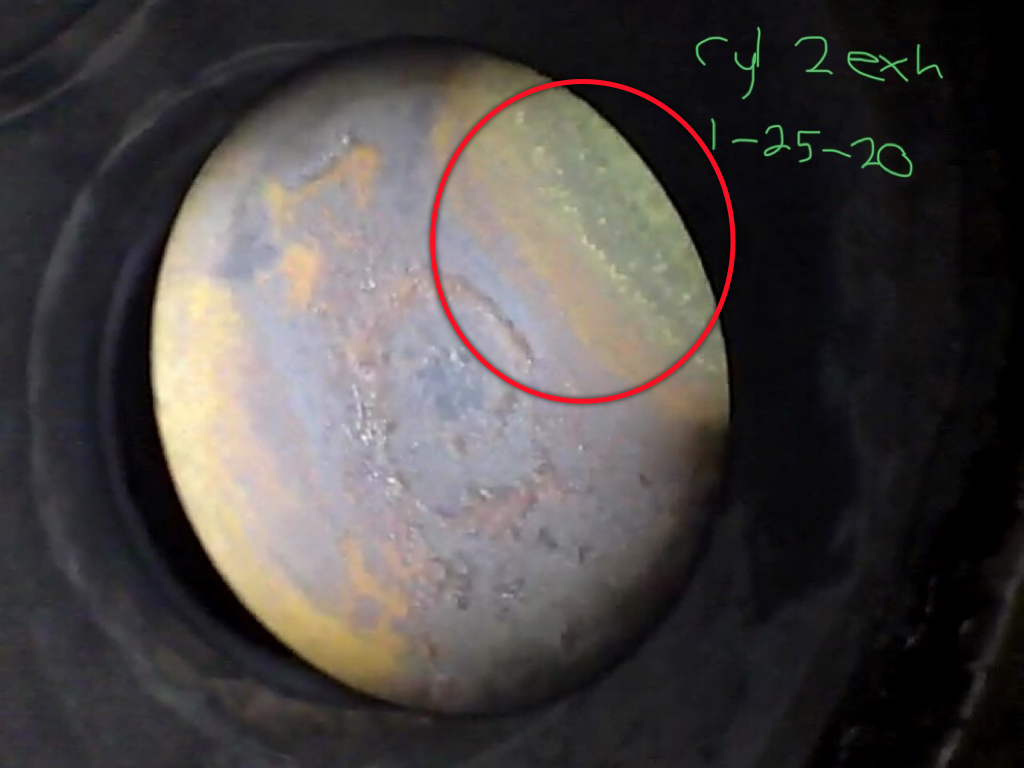
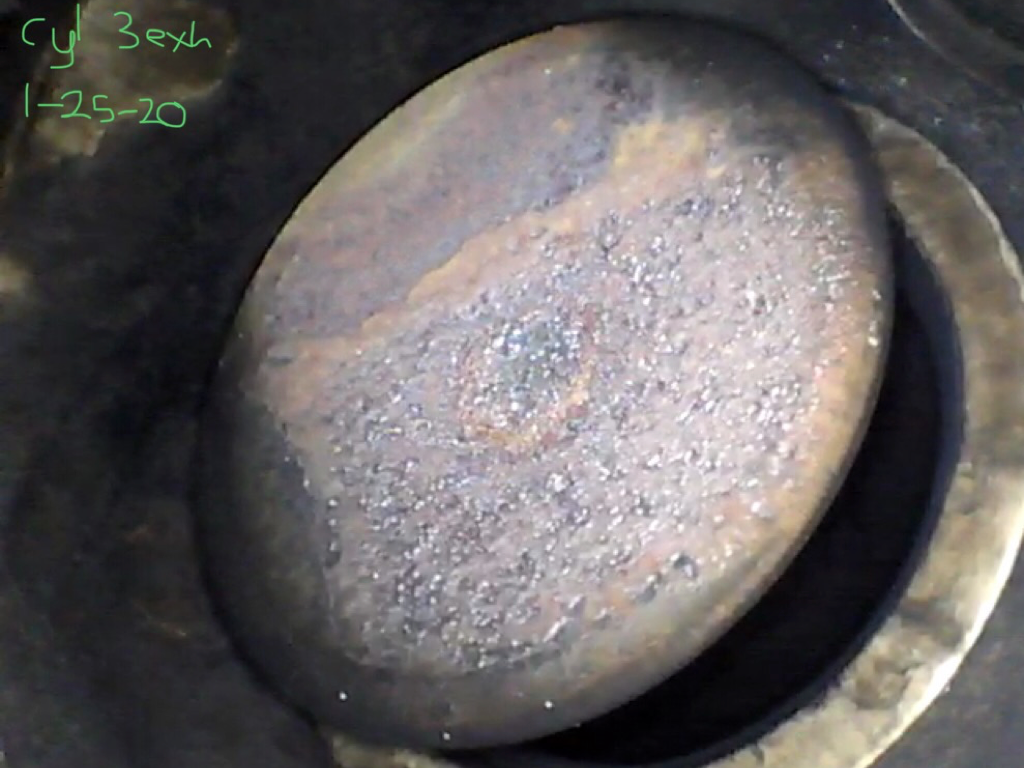
(Previous three photos courtesy of Sylvan Martin.)
Jason Figueroa had to change a cylinder on his Cherokee 235’s Lycoming O-540 engine due to a burning exhaust valve that was found with a borescope.
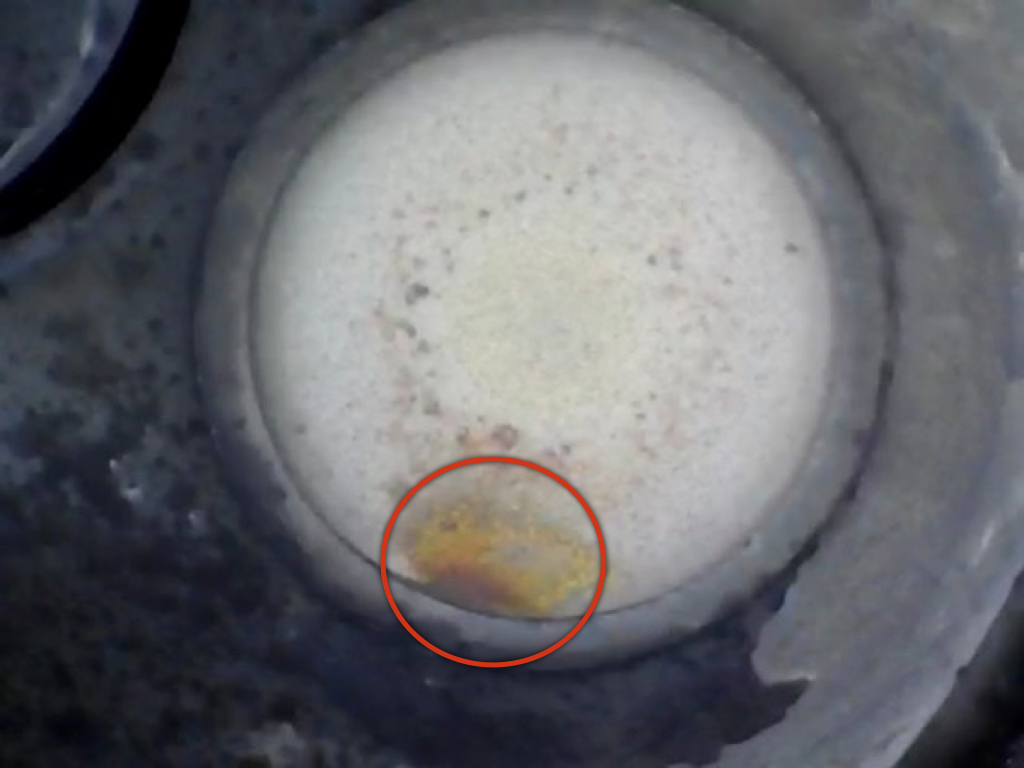
(Photo courtesy of Jason Figueroa.)
Jason said, “Borescoping told us we had an impending problem, and led to catching it before it failed.”
Here are two more exhast valve pictures from an unidentified source:
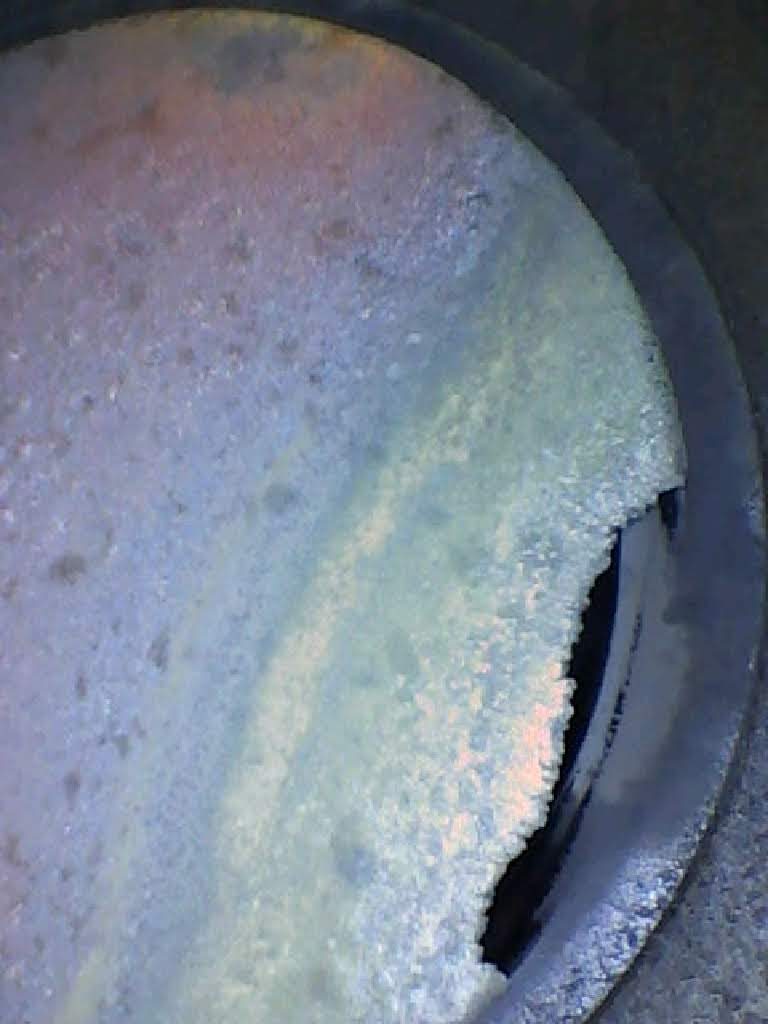
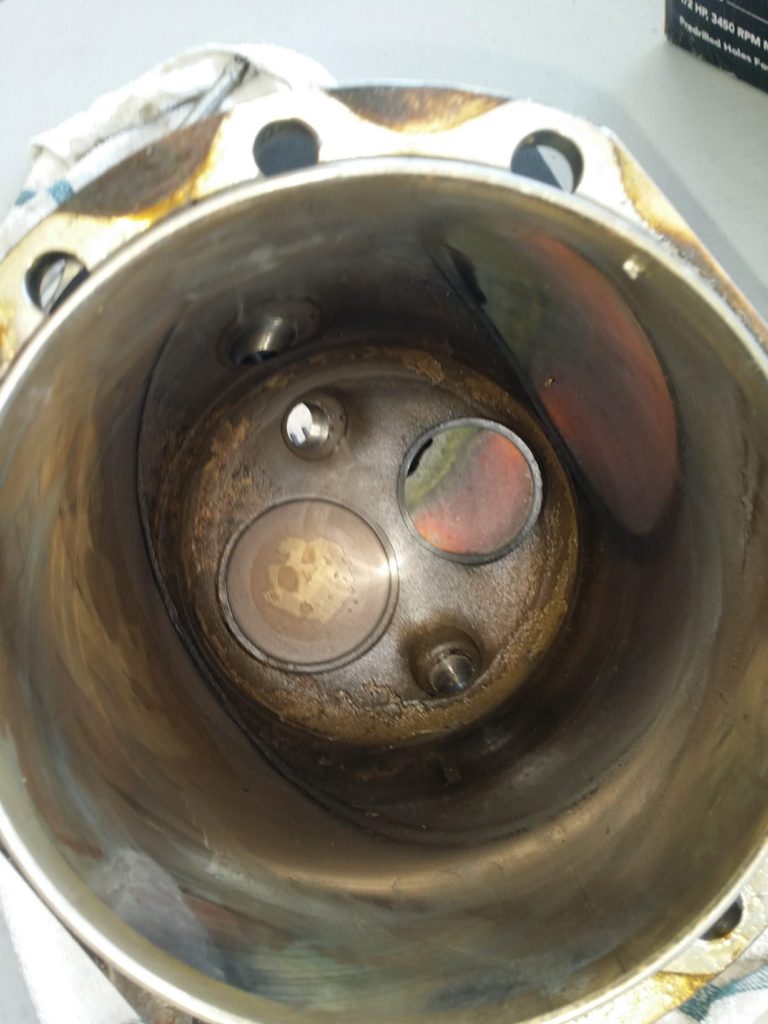
I’m convinced this broken valve could have been detected with a borescope LONG BEFORE the edge broke off.
My hope is that all of us who have the responsibility of determining the airworthiness of piston engines in airplanes, will use a borescope along with the compression tester for higher levels of safety and reliability.
Do you have a dream to fly? If so, you might be encouraged by the poem I shared at the end of my talk yesterday. My daughter sent it to me one day last Summer… it’s called, “The Dream Does Not Die!” If you’re interested, be sure to listen to the last part of the audio.
Recent Comments